On
New Year's Day, 2006, I acquired a Henry 13.56 MHz RF
Generator....and converted it over the following 6 months as
shown on this page.
Rear view of the Henry 3000D
converted to 6m. Note the 50k cutoff resistor and 12 VDC
zener diode mounted on the back panel. You can also see
the new 7/16 DIN RF connector installed in the rear of the Tank
Compartment. No RF is run under the chassis in that half
of the amplifier.
Top view of the tank compartment
from the rear of the RF deck. The blocking capacitors used
were a pair of 200 pF attached to a copper strap that is silver
soldered to the anode clamp. The coil side of the
connection is to a silver plated brass plate, with the coil
silver soldered to it. A pair of 50 pF blocking capacitors
were tried, but this circuit would not resonate because the slug
could not be pulled far enough back out of the main tuning coil,
and the loading capacitor needed more capacitance. Using a
pair of 500 pF blocking capacitors required that the slug be
inserted about halfway into the coil. Using a pair of 200
pF blocking capacitors seemed to work just as well, and only
required the slug to be inserted about 1/4 of the way into the
large tank coil.
The B+ is delivered to the tube
via the copper strap, that simply is held underneath the anode
clamp. The RF choke was the one that came with the 14 MHz
RF deck, except that only the wide spaced turns are used - the
rest of the choke was cut off so the choke was shortened, and
the end support bracket was moved several inches toward the rear
of the RF deck (as you can see in the photo, in which the two
original mounting screws for the RF choke support bracket are
still plainly visible). The final RF choke was 42 turns of
#18 enamel wire on a .7" diameter Teflon form, 2.75" long.
A pair of right angle drives turn a 1/4-20 threaded brass rod,
that moves the copper shorting slug into the coil for
tuning. Unit is shown tuned to 50.150 MHz. The 1.75"
OD copper tuning slug has Teflon plugs in each end, fastened
with a brass screw running through the slug. A 9/32" O.D.
piece of brass hobby tubing (held in place by 1/4" O.D. brass
rod running through it) supports the slug by running through the
top of it. The slug is moved back and forth by
turning a threaded brass rod that goes through the center of the
slug. The threaded brass rod goes through a panel
bearing with a 1/4-20 brass nut silver soldered to it, which is
mounted on a bracket silver
soldered to the inside center of the 1.75" long slug. The threaded
brass rod and the 1/4" brass support rod are insulated
from ground, and supported by the two HDPE end plates.
Overall view of the RF deck from
the top. The coil was made by using almost two of the
turns of the standard 14 MHz coil that came with the 3000D (1/2"
diameter tubing, 3.25" ID, 3" long). The L coil was
similarly made by using 3 turns from the original L coil
(3/16"diameter tubing, 1.5"ID). The original tuning shaft
was left in its same location after removing the flapper tuning
mechanism that came in the 14 MHz unit. The original
loading capacitor was used without any changes, except that the
fixed doorknob capacitors in parallel with the variable
capacitor (located under the silver plated brass plate at the
right end of the coil) were changed from 4 capacitors to 3
capacitors (two 33 pF and one 25 pF). Instead of an RF
choke on the output connector, I used a shorted quarter
wavelength of Teflon coax to provide additional second harmonic
attenuation. The initial test setup for checking out the
tank circuit was to temporarily place an 1800 ohm carbon
resistor between the tube's plate and chassis ground, and then
connect an MFJ-259 Antenna Analyzer to the output
connector.
In the original RF deck, there were two ceramic standoffs that
pushed down from the perforated cover onto the cooling fins of
the tube to hold it in place. I replaced these with
a single teflon spacer between the cover and the center of the
anode, so there would not be any obstruction air passing through
the cooling fins.
The variable inductor is probably
the most usual part of the RF Deck modification.
Hopefully, these notes will help anyone who is interested
to understand what I did, so they can more easily get started on
their own construction. Two 1/2" thick HDPE 4" wide by 6"
high end plates were used to support the slug assembly as it
moves into the coil to reduce the inductance and tune the tank
circuit. The end plates were spaced 6" apart and secured
to the chassis with angle aluminum brackets or the right angle
drive assembly; they were mounted 3/4" out away from the front
insdie panel of the RF Deck. The HDPE end plate next to
the loading capacitor is actually only 3" wide on the bottom -
it has a 1" x 3" notch cut out of it to provide clearance for
the connector plate and fixed doorknob capacitors between the
loading capacitor and the tank coil.
The slug shafts were located so
the 1-3/4" long slug (which is 1-3/4" in diamater) runs through
the centerline of the tank coil, which is 3-1/2" above the
bottom of the plate compartment. The threaded rod goes
through the center of the slug, and the brass hobby tubing for
support and alignment runs through the slug 1/2" above it.
The threaded rod goes through bushings on each HDPE end plate,
and is kept from moving back and forth by the flexible coupling
connection it to the right angle drive assembly and by the
locked double nuts on the far end of the shaft. The
alignment tubing is held betwee the two HDPE end plates by 1/4"
brass washers that go over the 1/4" brass rod that runs through
the alignment tubing and is secured on the outside of the HDPE
end plates by cotter pins. If you have more clearance, you
could also use 1/4" brass threaded rod with nuts on each end to
secure the alignment tubing. An extra piece of teflon
sheet was inserted between the variable loading capacitor plate
and the HDPE end piece to prevent arcing off the ends of the
brass rod which extends through the end piece to secure it.
The
T match input arrangement is shown above. The input
tuning capacitor is a half-meshed 100 pF unit. Both L1
and L2 coils are 6 turns of #14 wire, 1/2" I.D, approximately
.75" long. The coupling capacitor from the
input connector is 1000 pF and the input coil L1 is wound on a
ceramic coil form with a brass slug. A small piece of 1/4" diameter
brass rod was silver soldered to the threaded adjustment shaft
of the adjustable ceramic coil form used for L1, to make the
brass slug.
The filament choke is #10 wire (5 bifilar wound turns) through
a pair of toroids I happened to have in the junkbox (with a
calculated voltage drop at 51 amps of about 0.2 VAC).
Input tuning is "set and forget" but I rigged up a small belt
drive system so I could tweak the input tuning capacitor when
the amp was in operation.
The initial test setup for checking the input circuit was to
temporarily place a 50 0hm carbon resistor between the little
standoff where L2 is supported and chassis ground and then
connect an MFJ-259 Antenna Analyzer to the input
connector. Both L1 and L2 were squeezed and spread and
L1 slug adjusted until the input impedance (with an aluminum
lid placed over the compartment) showed a purely resistive 50
match, centered on 50.150.
The amp easily delivers 1500w
output with under 100w drive. The advantages of this amp
are:
1. You never
have to worry about over driving it.
2. It is
instant on, with no warm-up time.
3. It has
plenty of capacity for full duty cycle such as the digital
modes.
4. With a
soft start on the filament, it should run forever at amateur
power levels (actually this may not even be necessary, since
the filament transformer probably already limits the inrush
current to the cold filament).
5. It
produces a very clean signal with no harmonics.
Some
of the other modifications which were performed to the entire
unit include:
1. The
over-current sensing circuit inside the amp was disabled.
2. The
rectifier diodes were replaced with 8 diode blocks from K2AW
(full wave bridge configuration with rectifier blocks in
parallel and equalization resistors).
3.
The driver power supply and driver were removed.
4.
Because the plate supply was changed to a capacitor input
filter, the preferred design for a transformer was one which
will provide 3300 VAC. The existing transformer was
replaced with a much larger transformer, which provides
3080 VAC. A "buck/boost" transformer was added to
increase the primary voltage to provide 5 kv DC B+ key down.
5.
The time delay relay to short out the heating element in one
side of the primary of the B+ transformer was changed from .5
second to 4 seconds; this time delay seems to be just
about right for the amount of capacitance used in the
filter.
6.
The B+ filter choke was removed, and 24 uF from 22
electrolytic capacitors in series (560 uF , 400 VDC each) was
added in parallel with a pair of 32 uF, 4500 VDC oil filled
filter capacitors wired in series for a total of 40 uF.
The electrolytic capacitors were sandwiched between two pieces
of 1/8" thick high density polyethylene sheet.
7.
The four 20,000 ohm bleeder resistors were replaced
with (22) five watt 51 k resistors (one across each
electrolytic).
8.
A 100 ohm 200 watt resistor was added in series with
one of the legs of the filament primary transformer, which
causes the tube filament to warm up at half voltage (around 3
vac). This resistor is shorted out after
approximately 5 seconds with a zero-crossing solid state
relay. However, this may be overkill, since the shorted
filament transformer very probably does not provide enough
inrush current to the cold filament to cause damage.
9.
A relay box was added inside the amp to control external
antenna relays, as well as to short out the 50 K cutoff
resistor and put the amp into XMIT mode when a high
impedance short to ground is provided from the station
sequencer. The relay box includes a 28 VDC power supply
(to run the external coaxial relays) as well as a 12 VDC
supply (to power the relays in the box). As can be
seen from the photo below, a switch was added on the front
panel, to select whether power was applied to the relay box
when (1) the 3CX3000 amp is plugged into the wall but not
necessarily running or switched in, (2) switched in and
operating with the B+ applied, or (3) the power to the
relay box can simply be turned off. Since the 28
VDC is used to power external coaxial antenna relays on
receive, it is usually left powered on whenever power is
switched on to the ham shack.
10.
A small variac was added to one leg of the filament primary
transformer so that the filament voltage could be adjusted
accurately.
11.
A
larger
blower was installed on the bottom of the RF deck. I
used an old blower (4" wide x 10" diameter) from a Jennair
stovetop, and mounted a 240 VAC 1/10 horsepower electric motor
to it. In addition, I added a high volume "sucking fan"
on top of the RF deck (to reduce back pressure on the blower
as well as draw cool air down into the the tank
compartment across the components there.
12.
An
outboard
RF Bias Switching box was added to the input of the amp (the
one I previously used on my 2m 8877 amp). With the RF
bias switching, there is virtually no idling current
during transmit mode, and the tube is placed back into cutoff
whenever there is no drive. This keeps the tube running
cooler on modes with less than 100% duty cycle.
13. The original 1.5 ohm 20w
wirewound "glitch resistor" between the B+ supply and the tube
anode was replaced with a 100 ohm, 100w wirewound, and mounted
on the plate transformer, directly in front of the cabinet
cooling fans.
The following additional photos illustrate how the amplifier
was configured:
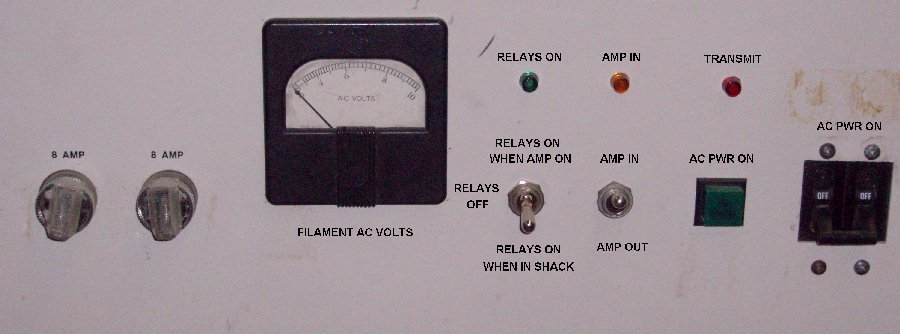
FRONT VIEWS
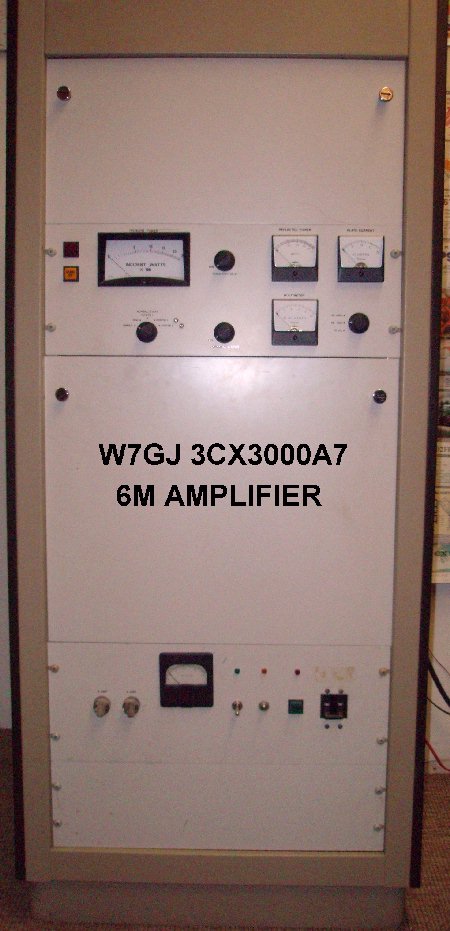

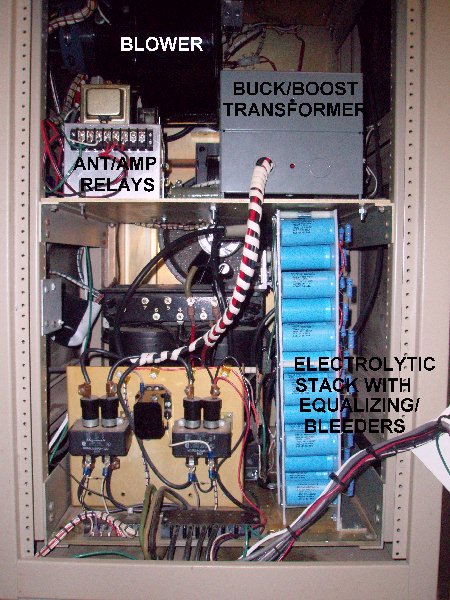
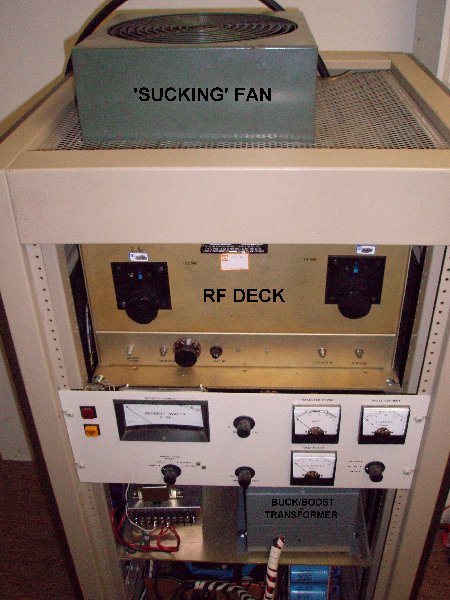
|
REAR VIEWS
Note - the original single 16 uF, 7500 VDC oil
filter capacitor pictured above was
later replaced with a pair of 32 uF, 4500 VDC
oil filled filter capacitors in series. The
new 100 ohm, 100w "glitch resistor" in the B+ line
was mounted on top of the plate
transformer.
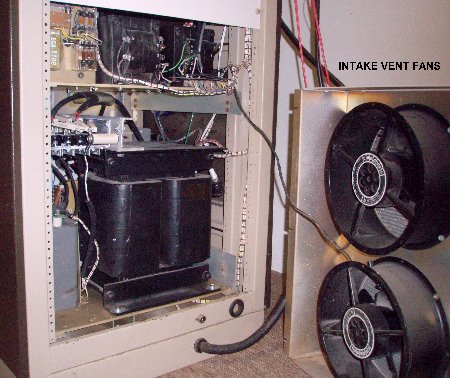
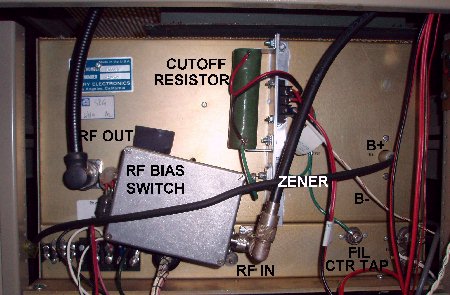
|
QRO 50 MHZ LOW PASS FILTER
|
This very heavy duty 50
MHz Low Pass Filter was constructed by using a pair
of 50 pF, 15 kVDC ceramic doorknob capacitors, and
three air wound self supporting coils.
The center coil ( L2
) is 6 turns, 2.5" long, using #6 AWG copper wire wound
on a 7/8" diamter form. Input and Output coils
( L1 and L3 ) are each 4 turns, 2'' long, using #6 AWG copper wire wound on a 3/4" diameter
form. The enclosure was built to fit the
space required for the coils. The box is 12"
long, 4" wide and 4.5" high. Baffles were mounted
around each capacitor to prevent enclosure
resonance at UHF harmonics.
Insertion loss was
measured at less than .06 dB, with attenuation
greater than 24 dB at 100 MHz.
|
 |
ADDITIONAL PHOTOS OF HOW OTHERS
HAVE DONE THE
6M MODIFICATION TO 14 MHZ & 27 MHZ UNITS
Revised 8 August, 2019